Springboard Biodiesel’s closed local loop biodiesel production system, called the CLL-1000 (CLL) is designed as a zero-waste, integrated, automated, multi-modular processing system. It allows an operator to produce the highest quality biodiesel from the lowest priced, regionally sourced feedstock.
Springboard’s CLL is designed around the concept that local, small-scale biodiesel production represents an attractive and under-served market opportunity. In the production of biodiesel, the cost of feedstock represents the largest cost to the producer, and because the most common, widely available feedstock sources are farmed crops such as soy, canola and palm oil – all more expensive in their raw form than the diesel fuel they are processed to replace – the commercial price of biodiesel has historically been higher than that of diesel fuel. More recently, the biodiesel industry has looked to less expensive feedstock sources, such as used cooking oil (UCO).
Springboard’s CLL can make 100% of its biodiesel from used cooking oil. The system processes multiple types of feedstock, however, and will create a cost advantage to the producer by locating the entire system at the source of the local, low cost feedstock.
Specifically, the CLL can process any vegetable and/or animal oil that is less than or equal to 10% Free Fatty Acid (FFA). FFA% is the measure of an organic oil’s degradation – the higher the number, the less that can be done to process it. The CLL’s 10% capability allows for a wider variety of feedstock sources than existing small-scale systems. Importantly, the feedstock flexibility allows for meaningful cost advantages to the user, as it can be placed near UCO collection facilities, chicken processing plants, fish processing plants and/or large farming operations (such as rice mills in northern CA). The physical proximity to the locally available feedstock and the subsequent “locally produced; locally consumed” nature of the CLL-produced biodiesel ensures that the owner/operator of the CLL will be making biodiesel with the lowest possible cost base.
Springboard’s CLL installation is located at 2323 Park Avenue, Suite 125 in Chico, California and is designed to produce 1,000 gallons of ASTM-D6751, B-100 biodiesel per 9 hour day and can be scaled up to make more based on available feedstock.
The footprint is compact – set within a 60’ x 80’ dedicated production area with an additional 2,500 square feet of dedicated outdoor tank storage space and required spill containment. Because the system is a fully closed loop system, with all separate production modules connected via industry standard pipe plumbing, and with all electrical connections appropriately grounded, it enables automated processing within the safest possible processing environment, assuring high quality fuel with a minimum of cost.
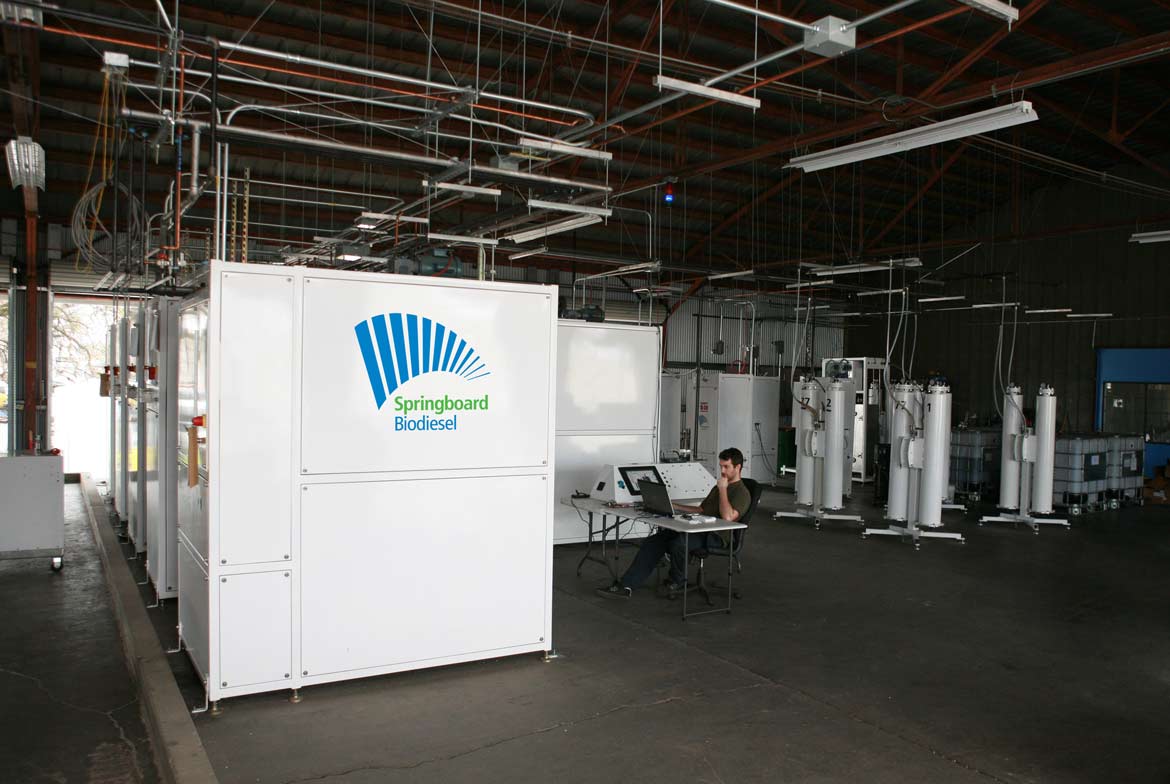
Specifications of the CLL System
- Process 1,000 gallons per day (extendible to 2,000 gallons if a second work shift is added)
- Compact footprint – less than 4,000 sq. ft. (1,200 sq. meters)
- Process veg/animal oil with a FFA percentage of up to 10% (vs. the 5% FFA that the Company’s family of BioPro can process)
- Eliminates over 7MM lbs. of CO2 annually
- Creates 525,000 Renewable Identification Numbers (RINS – currently trading in a range of $0.85-$0.90 per RIN – USA only)
- Potential to recapture glycerin of 85%+ purity (additional revenue stream)
- Waste-free production and recaptured process ingredients (methanol) assures lowest cost of production
- No water used
- Turnkey system with automated processing and redundant process controls
- Repeatable ASTM-D6571 results
- Proprietary design with multiple patentable aspects
- System allows for rapid payback and compelling project IRR
In mid-2012, Springboard was awarded a matching grant from the California Energy Commission (CEC) of $758,200. The grant was awarded under the CEC’s Alternative and Renewable Fuel and Vehicle Technology Program, and has helped establish the company’s first production CLL in Chico, CA.
Springboard Biodiesel is not aware of a comparably functional small-scale biodiesel processing system.
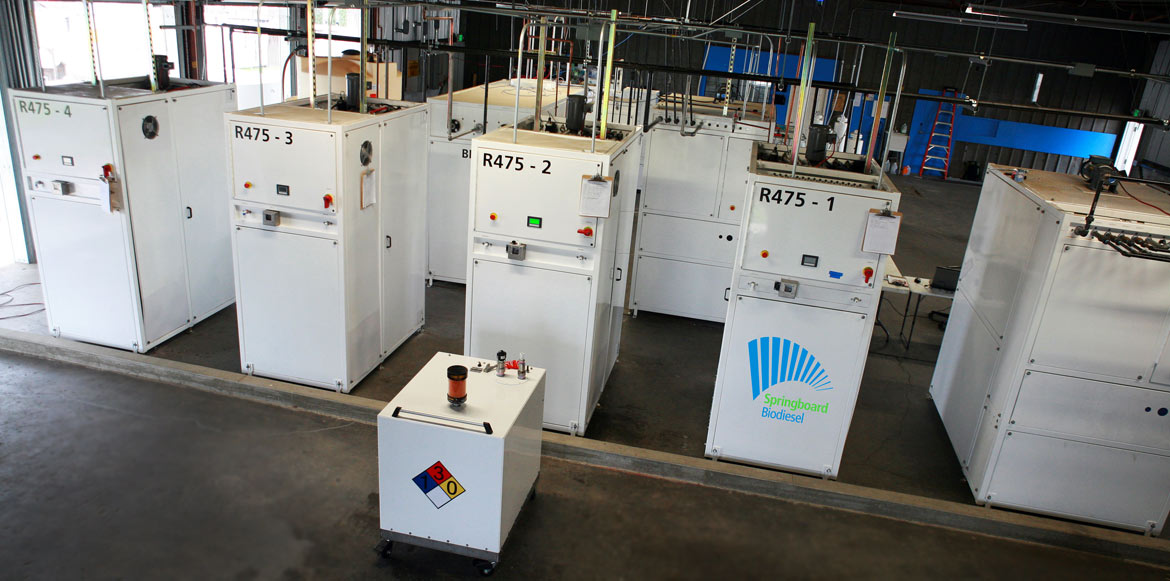
Modular Design Ensures Customer Flexibility
The CLL has been designed as a modular system that can be customized to the specific requirements (capacity) of the operator. Springboard Biodiesel’s base configuration will be 1,000 gallons per day in a two-shift (or staggered single shift) work schedule. This can be increased or halved, depending on the operator’s economic model and feedstock access. Below is a description of each of the modules:
Coarse storage: The basic system will produce 1,000 gallons over the course of 24 hours and necessitates a 9 hour work day – load first 500 gallons in the morning and the next 500 gallons before leaving for the evening.
It is assumed that the operator will store approximately one week’s worth of raw vegetable oil and one week’s worth of finished biodiesel and will store 3,500 gallons of methanol (assuring bulk pricing discounts). The raw vegetable oil will arrive at the facility at 10% or less FFA, 2% MIU.
Pre-processing unit: This further processes the oil, heating it up to 200ºF and dramatically reducing the MIU.
First oil buffer: This is a 700 gallon tank that is continuously filled by the preprocessing unit and emptied into the four (4) 125 gallon reactor units every 8 hours.
Reactor units: Under vacuum the oil (up to 10% FFA) is heated and then reacted into raw biodiesel and glycerin. During the reaction the reactors are interfacing with a large condensing unit that is simultaneously condensing methanol and water vapors (all recaptured methanol is re-purified and re-used in subsequent batches).
Waterless filtration prep units: Similar to the company’s SpringPro™ T76, these dual column filtration units treat the raw biodiesel prior to introduction to the demethylation skid. The media is relatively inexpensive, focused on the removal of soaps and other non-methanol related trace contaminants, and safely land-fillable upon exhaustion.
Demethylation skid: Comprised of three (3) separate modules, this skid removes the trace methanol from the glycerin, leaving the glycerin at approximately 90% purity and producing as a by-product salt (NaCl) and high FFA% oil that will later be used as a source of heat (in-line boiler); it will remove the methanol from the raw biodiesel – without the use of water. This skid is comprised of the BD-380, the G-190 and the MC-12.
Post processing unit: The unfinished biodiesel is circulated through a post processing system, enabling a final “polish” and ensuring ASTM cold-soak compatibility.
Methanol recovery nit: This is a purification station that takes the recovered “dirty” methanol and return it to 99.8+% purity, enabling a lower cost of goods for the next batch of biodiesel.
System Iintegration module: The entire system is fully automated, with redundant process controls and the ability to remotely monitor the systems during operation.
History
Back in 2014, the CLL was first turned on. It produced nearly a quarter of a million gallons of ASTM-D651 grade biodiesel. The Company’s goal was to locate defined CLL “nodes” throughout California and beyond and network these nodes. Unfortunately, in 2016, the cost of diesel dropped to 12 year lows in California. The CLL was "mothballed" and ownership is now seeking a buyer interested in benefiting from this equipment.
Any business that feeds people or produces waste vegetable or animal oil and is interested in establishing a new revenue stream or significantly improving its operating margins, is encouraged to contact Springboard Biodiesel to discuss.
The CLL’s processing flexibility, environmental impact and rapid economic benefits create an excellent platform upon which to rapidly build a large network of, local biodiesel production facilities, both in the US and internationally.